Jurong Port (JP) officially opened its Ready-Mixed Concrete (RMC) Ecosystem on Wednesday (27 November), reaching a major milestone in the development of Singapore’s first Integrated Construction Park (ICP).
JP’s strategic location at the nexus of the construction supply chain, coupled with its public port status and expertise in port logistics, makes it a natural choice for developing a comprehensive ICP. Expected to be completed by 2030, the entire complex will integrate JP’s existing cement terminal, the new RMC Ecosystem, the future Steel Ecosystem, and the future Integrated Construction and Prefabrication Hub (ICPH).
With JP serving as the key landing point for seaborne importation of vital construction materials, locating the ICP at the port enables the aggregation of raw materials like cement, construction aggregates (sand and granite) and steel. Such a set-up facilitates the seamless manufacturing of precast components and modules within the port. By housing different construction facilities such as terminals, storage yards and RMC batching plants together, JP enhances the collaboration among industry players in the built environment sector, optimising land use and integrating synergistic activities into a comprehensive construction park.
“This is the first Integrated Construction Park that we are establishing in Singapore. We have moved from open precast yards (OPYs) to Integrated Construction and Prefabrication Hubs (ICPHs), to ICPs now,” said Desmond Lee, Singapore’s Minister for National Development, speaking at the RMC Ecosystem opening ceremony on Wednesday.
“This marks a significant milestone for the built environment sector as we move towards an advanced manufacturing environment. This also advances our ambitions for improved productivity, resilience and sustainability under the Built Environment Industry Transformation Map.”
Innovative RMC Ecosystem
Covering a land area of 11.9 ha, JP’s RMC Ecosystem enables the efficient discharge of construction inputs directly into a cluster of downstream construction-related activities. It also creates economies of scale, enabling common non-core activities to be pooled into shared services, for example centralised recycling, truck washing and logistics planning. The pooling of such services will substantially lower costs and facilitate adoption of new technologies, thus allowing industry players to focus on their core business activities – such as batching concrete – and increase their competitiveness.
“These shared facilities free up usable land area for production activities within each RMC firm’s plot, allowing them to use up to 80% of their land for RMC production. This is a vast improvement from the previous 40% utilisation when land plots were developed in silo,” explained Mr Lee. “With improved productivity, the RMC batching plants at the Jurong Port ICP are now able to produce 45,000 cu m of concrete per plant each month. This is an impressive 50% improvement compared to their previous capacity, and will support the projected demand for concrete in the western region of Singapore.”
A distinctive feature of the RMC Ecosystem is its automated, enclosed conveyor system. It is used to “transport sand and granite directly from the wharf to the storage areas and RMC batching plants, without the need for transport via trucks,” noted Mr Lee. “This innovative system, the first of its kind in Singapore for material transfers, saves us more than a million truck-trips each year. This is a move in the right direction, towards improved operational efficiency and environmental sustainability.”
According to JP, construction of the S$200 million RMC project began in September 2020 and it has been operational since October 2023. The new facility saves up to 8 ha of land, which can be repurposed for other national priorities. Apart from eliminating more than 1,000,000 unnecessary truck trips annually, aggregates vessel can now berth directly at JP, eliminating the need for 216 barge trips annually. This translates to a reduction of 23,500 t of CO2 emissions per year.
The installation of solar panels on the rooftop of the RMC Ecosystem also has the potential to generate up to 6.8 GWh of solar power each year, added JP. This will help offset around 50% of RMC Ecosystem’s annual electricity consumption from the grid and reduce operational carbon footprint by close to 1,800 tCO2.
The RMC Ecosystem offers a 30-year lease, encouraging its tenants to invest in advanced technologies instead of settling for short-term arrangements. JP said a total of 11 aggregate plots, comprising six plots at the common storage area and five plots integrated with RMC plants, have all been fully occupied.
“The ICP is the first of its kind and it will boost operational efficiency across the construction supply chain. The RMC Ecosystem is designed to optimise land use while enabling concrete producers like Pan-United to better serve development projects in the west of Singapore,” shared Ken Loh, CEO of Pan-United Corporation Ltd, a well-known player in the industry and one of the RMC Ecosystem tenants.
Speaking to SEAC, Mr Loh highlighted that “cement supply, aggregate importation and RMC plants are all at the same location now. This creates an efficient supply chain that reduces trucking logistics and improves land utilisation. With our RMC batching plant located close to our cement terminals, we instantly have access to our cement supply right at our doorstep.”
On the sustainability front, Mr Loh said, “The new Park is more environmentally friendly by removing the use of trucks and the fully enclosed conveyors will reduce dust pollution. Furthermore, BCA’s standards for new RMC plants will better control air and water pollution. All these features will enhance the working environment and improve operational efficiency.”
Besides Pan-United, the other RMC Ecosystem tenants are Island Concrete, Sinmix, Star Ready Mix Concrete, Top-Mix Concrete, YTL Concrete and Alliance Concrete (the latter will join in mid-2027), as well as HL Building Materials, Orient Natural Resources and Prospaq.
“Jurong Port is encouraged by the industry’s support for our RMC project,” commented Terence Seow, CEO of Jurong Port. “This success reflects the industry’s trust in our commitment to enhance productivity, resilience and sustainability for the construction supply chain. We did not undertake this transformative journey on our own, but worked closely with various government agencies and industry partners to collectively innovate, revamp and relocate a well-entrenched RMC supply chain to be adjacent to the waterfront.”
Multi-tenant ICPH
Situated in close proximity to the RMC Ecosystem and the future Steel Ecosystem, JP’s ICPH will eliminate the need for precasters to set up their own concrete batching plant and steel mesh fabrication systems. By leveraging on this construction ecosystems (RMC, steel and cement), the construction of precast components and modules could take place in the form of an efficient ‘assembly line’ at JP. This will significantly reduce double handling and land-take, as well as help to decarbonise the supply chain.
The ICPH is scheduled for completion in 2027 and will utilise a multi-tenancy model that increases land utilisation. JP said three local precasters have expressed their interest in this ICPH, taking up three of the four floors. The facility will offer a 25 year-lease, helping to foster technology investment among industry players.
JP further mentioned that the ICPH will also enable the investment in and installation of solar panels on the rooftop of the building, which can generate up to 2.3 GWh of solar power per year. This has the potential to offset around 50% of ICPH’s annual electricity consumption from the grid and reduce operational carbon footprint by close to 550 tCO2.
Moving forward, the government will “continue to develop more ICPs around Singapore, such as at Pulau Punggol Barat,” said Mr Lee. “These new ICPs will enable more construction firms to reap the benefits from the ecosystem of advanced technologies, logistical efficiencies and co-located synergistic construction facilities.”
Mr Lee pointed out that “with the use of automation and technology within the ICP, we also require a more skilled workforce to operate, supervise and manage these advanced systems. New jobs will be created within ICPs for specific roles such as technical specialists and supply chain managers.
“I strongly encourage professionals in the built environment sector to continuously upskill and equip yourselves with the knowledge and capabilities to tap on emerging technology. This proactive approach will put you in good stead to thrive in a constantly evolving sector.”
Images 2, 3 & 5: Jurong Port
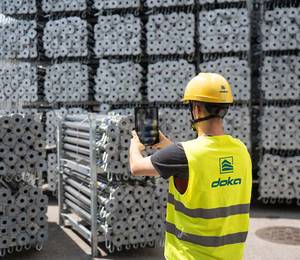
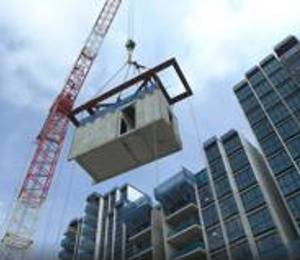
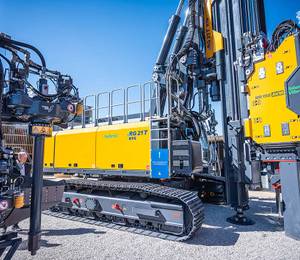
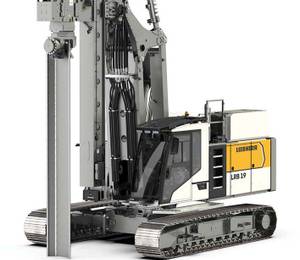
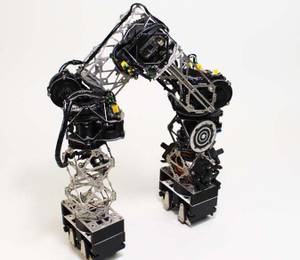
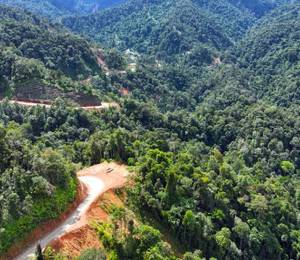
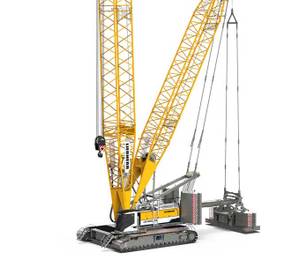