The new shuttering robot from Elematic is designed to optimise the automated production of double wall elements. The company’s technology can cater for all types of wall production, including solid wall, sandwich wall and filigran concrete elements.
And, like those reliable and efficient circulation lines for sandwich wall production, the new Edge Double Wall offers the same high-quality fundamental characteristics, said Toni Koitmaa, product director at Elematic. “The double wall plant includes much of the technology that is also found in our sandwich and solid wall circulation lines, based on years of experience.”
With everything from design to assembly, including automation and software produced by the company, customers can now enjoy greater functionality and efficiency of their plants, especially when using Elematic Plant Control, a production operations management software suite that is specially designed for precast concrete factories.
Shutter stay or shutter go
The new shuttering and deshuttering robot demonstrates the ease and accuracy with which shuttering can be placed on the table, whether it is taken from active or passive storage. Incorporating the latest movement control system for improved controllability and efficiency, the robot is able to rapidly move the shutters, before placing them with pinpoint accuracy, to ensure superbly straight-edged wall panels with sharp 90° corners.
When the time comes for deshuttering, the new robot can also perform that task when required, depending on phase time, or, alternatively, a separate deshuttering robot may be used.
“The new robot is very precise. Its robust structure and tracks manufactured to strict tolerances guarantee that vibration, swaying and movement deviations are kept to a minimum,” added Mr Koitmaa. “Not only is the robot accurate, it is also fast, durable and economic.
“The intelligent automation keeps the movement speeds optimised, saving energy while still placing the shutters as fast as possible. Our customers can be assured of producing a consistent quality of wall panels, along with safer working methods, lower production costs and satisfied customers who appreciate the straight edges.”
Improve quality and quantity
Elematic’s Plant Control technology highlights how digitalisation is able to streamline factory automation and work processes and deliver major improvements in production efficiency and profitability, resulting in a smooth workflow without unnecessary stops, human errors and material waste.
Easily integrated into the IT systems of existing precast factories, this software suite covers both floor and wall production, with Plant Control Wall Quality module being an ideal tool to decrease operational costs and improve quality, of sandwich wall production in particular.
Decreasing the time-consuming and manual quality-control tasks common at many factories, Plant Control Wall digitalises the process and recommends the panels for checking – a big time saving on the 100 products each day that may need manual checks at an average facility.
Using the automatically stored production history data, the work processes where issues occurred can easily be identified and reviewed, allowing quality improvement actions to be easily taken. Instead of merely collecting data to satisfy legislators and customers, it can now be used to improve the production process too.
“You can easily find the five main issues that required correction work one month, improve your process the next and then compare how many similar faults you’ve had before determining the next month’s top five issues,” said Jarkko Salmensivu, director, software business unit at Elematic.
“You’re now focusing on reducing quality errors to minimise fixing time. Once you know what the key problems are, it might only take a short time to fix the process – fixing the finished panels will take much longer!”
Working alongside other Elematic wall production solutions, the FaME magnet shuttering solution provides yet another example of the company’s emphasis on resource efficiency, with the use of recyclable aluminium side profiles providing a sustainable alternative to the commonly used wood side forms that are thrown away after usage, or heavier steel solutions.
Easy to attach and to remove from table surfaces, with no need for welding, bolting or grinding, FaMe magnet shuttering reduces the cost of production, while handling most wall thicknesses, from 70 – 500 mm, with accessories even up to 800 mm.
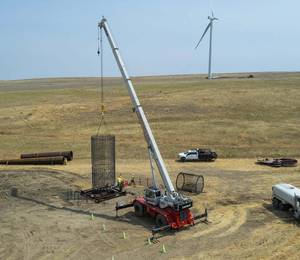
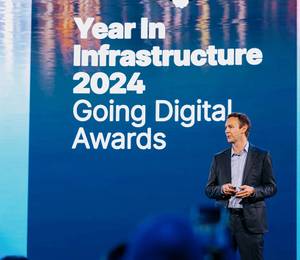
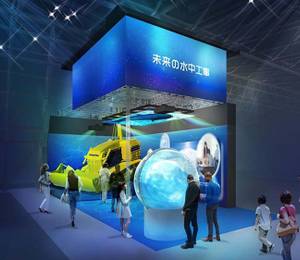
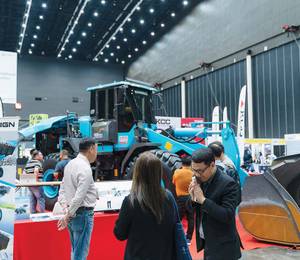
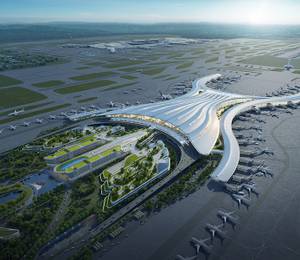
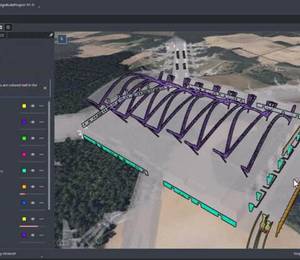
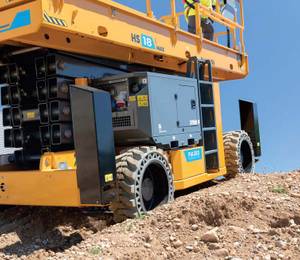
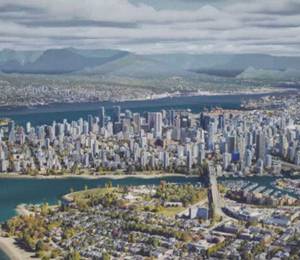
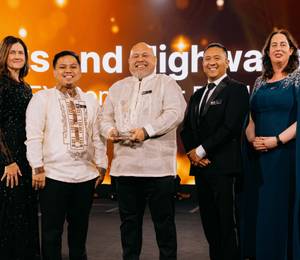
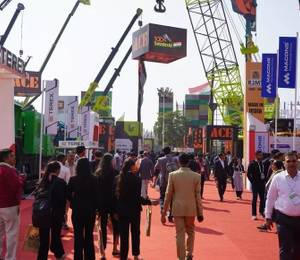