Elematic is set to unveil its latest double-wall shuttering robot, along with a series of slab saws, automatic transport wagons and services that boost efficiency and safety, while reducing waste.
The all-new shuttering robot is designed for solid wall, double wall and filigran concrete element production. The robot is the latest part in Elematic’s whole precast concrete plant automation technology offering.
The company, already a leader in hollow core floors and sandwich construction walls, is now expanding its wall offering to include state-of-the-art double wall elements. When coupled with its robot control system and whole-factory Plant Control system, Elematic can deliver optimised automation to achieve the best precast factory layouts and processes for specific customer needs.
At the heart of this modernisation is Plant Control, a suite of software that combines precast process optimisation with the latest IT. A central element of the shift to automation, and paperless production processes, the system streamlines operations, workflows and minimises errors.
Capacity, material and storage management, transport and production planning, as well as a host of other services, Plant Control makes sense of fluid and complex precast factory’s operations. Placing wall shuttering has never been so easy.
Elematic said the robot on display at bauma will demonstrate the ease and accuracy of placing shuttering. Thanks to its use of lightweight shutters, the robot can move faster and place shutters using powerful magnets with far greater accuracy. The robot also incorporates the latest movement control system, improving the controllability and efficiency of the robot.
In addition, the Extruder E9 from Elematic is used to cast hollow core floor slabs. It works hand-in-hand with the Modifier E9, a computer-controlled unit for creating openings during the casting process.
The Modifier E9 can automatically dig, plot and drill holes in double quick time, with the removed concrete automatically recycled into the Extruder E9 – with zero waste. Not only can this reduce the CO2 emissions of an average factory by an impressive 1,000 annually, it can also offer that same average factory savings of €135,000 a year, according to Elematic.
New saw family
In addition, bauma will see a new family of floor slab saws unveiled. The multi-purpose Sawpreparer S5 not only cleans the slab before cutting – it can also pull the pre-stressing strands (each one of which can weigh 100 kg) along the slab, reducing the need for manual pulling.
Now with a simpler mechanism and reduced height to fit in lower production halls, the easy maintenance Sawpreparer can also cut slabs 100 mm deeper, at 500 mm, and at multiple angles. The blade is now shielded by a telescopic cover – which lowers noise and blocks the progress of flying pieces from cutting.
Another new saw is the semi-automatic P7. Like the Sawpreparer, the P7 has a simpler and more reliable mechanism and a telescopic blade cover. It can cut up to 500 mm and has a new blade movement and drive mechanism for easier maintenance. It also has a reduced height and features an updated control system, with intuitive user interfaces and improved cutting control programmes.
The bigger saw E9 – which is fully automatic – cuts to a depth of 500 mm as well and shares all of the same upgrades. Both the P7 and E9 saws are available with much improved dust suppression. The classification for the filter is HEPA 13, which means that the dust-filled air of the cutting process is effectively captured, filtered and returned to the factory environment in a very clean condition.
Cutting, drilling and forming openings all have the potential to create bottlenecks in the production flow of a precast plant. But drilling-on-the-go is a prospect of Elematic’s all-new Drillbeam E9. Not only can it lift the slabs from the bed onto transport wagons, its three in-built drills can simultaneously and accurately drill the numerous weep holes that are required in hollow core floors. It can drill from below, at the ends and – unusually – in the middle of the slab.
What’s more, Elematic will be launching a fully automatic slab transportation system – the Wagon E9-. Its zero-emission battery drive makes pulling cables unnecessary and all that is needed is to load the slab onto a wagon at each end and they will take the slab off to storage – with no need for human intervention. The Wagon E9 is guided by radars that ensure safety, and the trucks can be easily integrated into both new and existing factories.
Bauma booth: B1.323
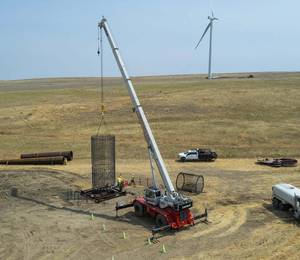
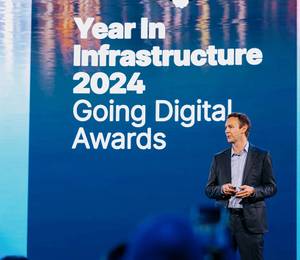
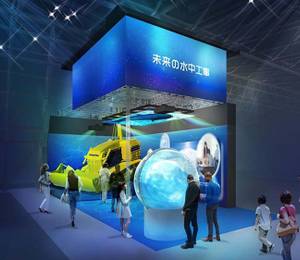
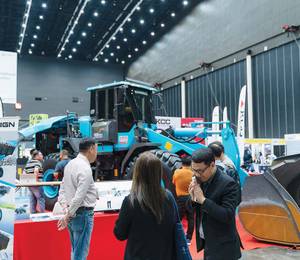
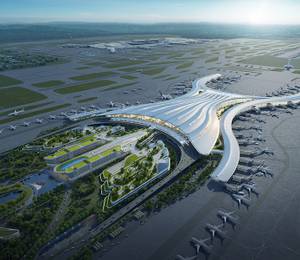
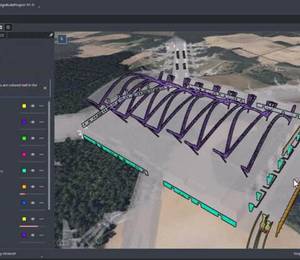
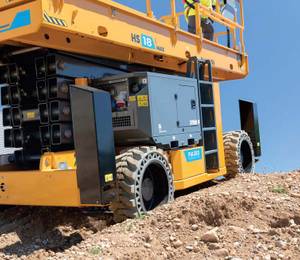
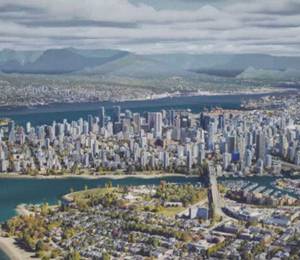
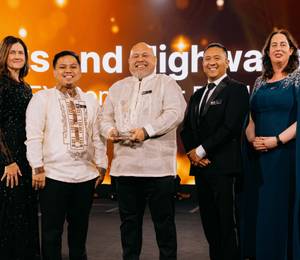
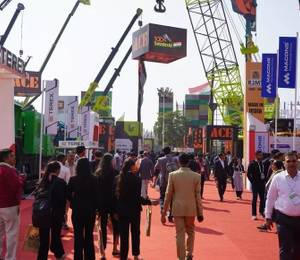