In the north of Taiwan, about 40 minutes from Taipei, the ChinPaoSan Necropolis cemetery is being extended with two new buildings: an arrival hall that will house tombs, a ceremonial place of worship, an auditorium and small museums; and a pavilion, which can accommodate up to 1,000 people on feast days.
The pavilion – named Oceanic Pavilion – features an iconic design combining pools of water with monumental, half cutaway spherical surfaces. The spherical shapes are said to symbolise the circle of life and the infinity of time, while the element of water achieves aesthetic closure.
ChinPaoSan Ltd (the developer) – which is also carrying out the construction work - has appointed Steven Holl Architects as architect on the project. The structural engineer is Guy Nordenson & Associates, with the local structural engineer TH Tsai & Associates. Transsolar has been commissioned as climate engineer, while Heng Kai Inc as mechanical engineer.
For construction of the arrival hall and the pavilion, Doka is supplying its formwork systems plus services from project management through logistics to on-site formwork instructor. The Doka systems chosen include the Top 50 large-area formwork, Framax Xlife framed formwork and Dokaflex timber-beam floor formwork.
Made-to-measure custom formwork built by the Doka Pre-assembly Service is also provided for the special spherical shapes. “Specifically, the angles of the conjunctions points between the spheres are unique and present artistic impulses from an architectural perspective,” said Tung-Ho Tsai, head of ChinPaoSan PCM consultancy. “Paradoxically, the simplicity of the design makes the construction complicated and challenging. However, Doka’s experienced engineering team met all the requirements from the architect. Additionally, the high safety standards are fulfilled.”
According to Doka, a 3D model was used during formwork planning in order to simplify the job. The points covered include the orientation of the profiled timber formers, the make-up of the formwork sheeting, and the ways and means of assembling the formwork.
Doka came up with a plug-in system, which was specially designed for the formwork of any 3D shapes. Timber formers, manufactured as a system of push-fit elements, are the basis for the free-form curving 3D formwork surface, explained Doka. The geometry data for these timber formers are transferred directly to the CNC (Computerised Numerical Control) spindle moulders and routers in the Doka Pre-assembly Service workshop. The push-fit system enables the timber formers to be locked together quickly and securely. Production is more efficient and assembly faster, said Doka, because less training is needed for the personnel.
Doka’s Dokaflex tables, TLS table lifting system and H20 formwork beams are also used in the project. Construction work started in 2014, and it is reportedly still ongoing.
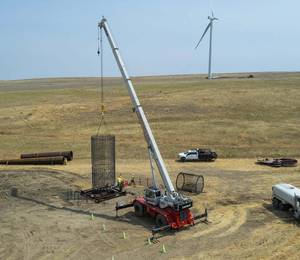
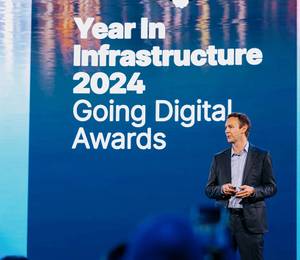
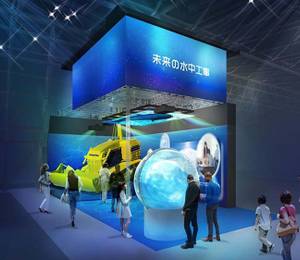
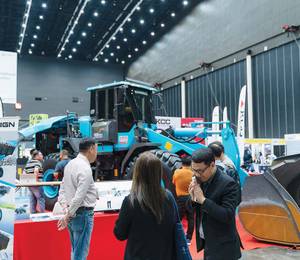
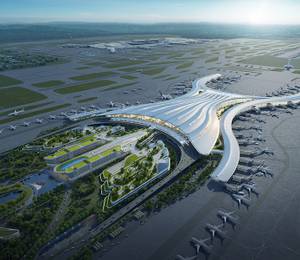
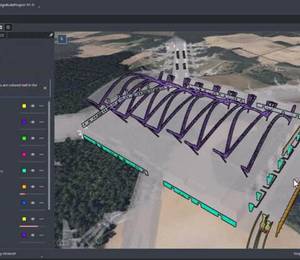
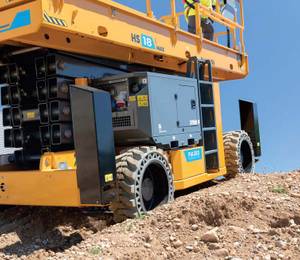
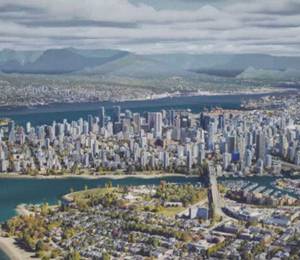
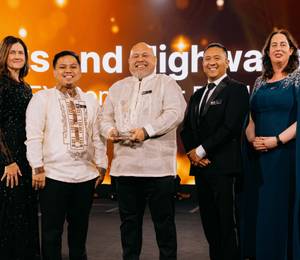
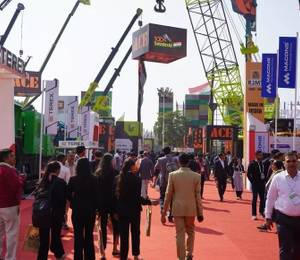